Top Components Machining Exporter Offers Quality Services
By:Admin
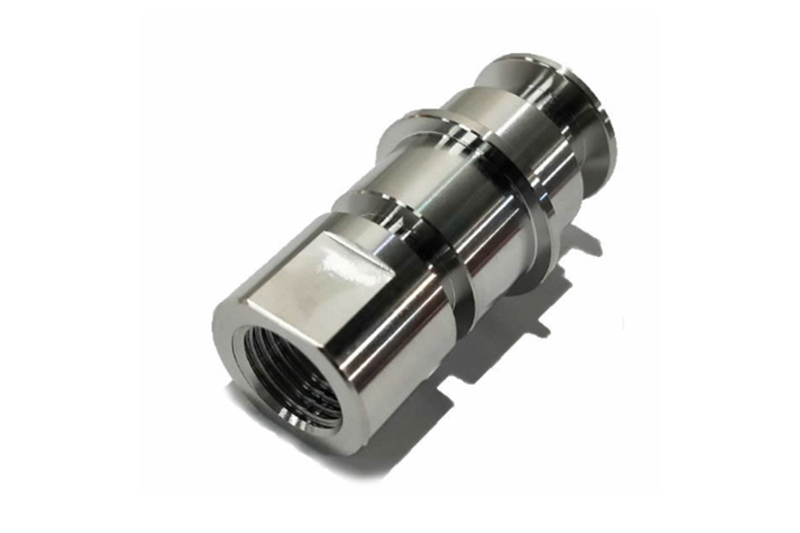
With more than 20 years of experience in the industry, Components Machining Exporter has built a strong reputation for its expertise in producing precision components for a wide range of industries, including automotive, aerospace, medical, and electronics. The company's commitment to quality, innovation, and customer satisfaction has enabled it to establish itself as a trusted supplier of precision components to leading global companies.
"We are pleased to announce that we have successfully expanded our export to new international markets," said the CEO of Components Machining Exporter. "This milestone further demonstrates our commitment to growth and diversification, as well as our ability to meet the evolving needs of our global customers."
Components Machining Exporter's success in exporting its products to new markets is a result of its dedication to continuous improvement and investment in cutting-edge technology. The company's state-of-the-art manufacturing facilities are equipped with advanced CNC machining centers, precision grinding machines, and coordinate measuring machines, allowing it to produce complex components to the highest standards of quality and precision.
In addition to its advanced manufacturing capabilities, Components Machining Exporter employs a team of highly skilled engineers and technicians who work closely with customers to develop custom solutions for their specific needs. This customer-centric approach, combined with the company's technical expertise, has been instrumental in its ability to expand into new international markets.
The company's commitment to international expansion is further underscored by its strong focus on compliance with international quality standards and regulatory requirements. Components Machining Exporter is certified to ISO 9001 and AS9100 standards, ensuring that its products meet the highest levels of quality and reliability for global customers.
As part of its export expansion strategy, Components Machining Exporter has also established strategic partnerships with leading international logistics providers to ensure the timely and efficient delivery of its products to customers worldwide. This streamlined approach to global logistics has helped the company overcome trade barriers and expand its market presence in new international markets.
Looking ahead, Components Machining Exporter remains committed to further expanding its global footprint and capitalizing on new opportunities in international markets. The company will continue to invest in technology, talent, and global partnerships to deliver innovative solutions and superior products to its customers worldwide.
In conclusion, Components Machining Exporter's successful expansion into new international markets is a testament to its relentless pursuit of excellence and its unwavering commitment to customer satisfaction. With a strong foundation built on quality, innovation, and expertise, the company is well-positioned to continue its growth and make a significant impact in the global market for precision components.
Company News & Blog
How to properly mold and create products using molds
Molding Mold, a leading provider of high-quality injection molds, recently announced the launch of their new state-of-the-art manufacturing facility. The company, known for its expertise in producing precision injection molds for a wide range of industries, has invested heavily in the new facility in order to meet the growing demand for their products and services.With over 20 years of experience in the industry, Molding Mold has established a strong reputation for delivering innovative and reliable solutions to their customers. Their team of highly skilled engineers and technicians work tirelessly to design and produce molds that meet the highest standards of quality and precision. The company's commitment to excellence has earned them the trust and loyalty of numerous clients, ranging from automotive and medical industries to consumer goods and electronics.The new manufacturing facility represents a significant milestone for Molding Mold, as it will enable the company to expand their production capacity and streamline their operations. Equipped with the latest technology and machinery, the facility is designed to enhance efficiency and productivity, allowing Molding Mold to fulfill large orders and deliver products within tight deadlines.In addition to increasing their production capacity, the new facility will also allow Molding Mold to further improve the quality of their molds. The company has implemented rigorous quality control measures to ensure that every mold that leaves their facility meets the highest standards of precision and performance. By leveraging advanced manufacturing techniques and processes, Molding Mold is able to produce molds that are not only durable and reliable, but also highly precise and consistent.The launch of the new manufacturing facility has generated a lot of excitement within the industry, as Molding Mold continues to demonstrate their commitment to innovation and excellence. The company's investment in cutting-edge technology and infrastructure is a testament to their dedication to meeting the evolving needs of their customers and maintaining their position as a leader in the market.In a statement regarding the new facility, the CEO of Molding Mold expressed his enthusiasm for the company's future prospects. "We are thrilled to inaugurate our new manufacturing facility, which represents a significant step forward for our company," he said. "With this state-of-the-art facility, we are well-positioned to meet the increasing demand for our products and services, while continuing to uphold the highest standards of quality and precision."As Molding Mold looks ahead to the future, they are confident that the new manufacturing facility will enable them to further strengthen their position in the industry and continue to provide their customers with exceptional solutions. The company remains committed to pushing the boundaries of innovation and technology, and the launch of the new facility is a testament to their unwavering dedication to excellence.With their proven track record of delivering high-quality molds and their ongoing investment in advanced manufacturing capabilities, Molding Mold is poised for continued success and growth in the years to come. As the company continues to expand its reach and capabilities, they are well-positioned to meet the evolving needs of their customers and remain a trusted partner for businesses across a wide range of industries.
DIY Guide: How to Anodize Aluminium at Home
Are you looking to give your aluminium products a sleek and professional finish? Look no further than the innovative technology offered by {} that allows you to anodize aluminium right in the comfort of your own home.With over 20 years of experience in the industry, {} has become a leading provider of anodizing solutions for both commercial and personal use. Their commitment to quality and innovation has led to the development of anodizing kits that are perfect for DIY enthusiasts and small businesses alike.The process of anodizing aluminium involves creating a durable and corrosion-resistant layer of aluminium oxide on the surface of the metal. This not only enhances the appearance of the aluminium but also provides added protection against wear and tear. Traditionally, anodizing has been a complex and expensive process that required specialized equipment and professional expertise. However, {} has revolutionized this industry by introducing anodizing kits that are simple, cost-effective, and easy to use.The {} anodizing kit comes with everything you need to get started, including the anodizing machine, power supply, anodizing solution, and comprehensive instructions. The compact and user-friendly design of the machine makes it perfect for home use, while still delivering professional-grade results. Whether you are looking to anodize small parts for your personal projects or want to offer anodizing services as part of your business, the {} kit is the perfect solution.The process itself is straightforward and can be completed in just a few simple steps. First, the aluminium part is thoroughly cleaned and degreased to ensure a smooth and even finish. It is then placed in the anodizing solution and connected to the power supply, which initiates the anodizing process. The machine's precise controls allow you to adjust the voltage and current to achieve the desired thickness and color of the anodized layer.One of the key advantages of the {} anodizing kit is its versatility. With the ability to anodize aluminium in a range of colors, you can customize the finish of your products to suit your aesthetic preferences. Whether you prefer a natural metallic look or want to experiment with bold and vibrant colors, the options are endless. This flexibility allows you to unleash your creativity and add a unique touch to your aluminium projects.In addition to its user-friendly design and customizable options, the {} anodizing kit also prides itself on its environmental friendliness. The anodizing process produces minimal waste and does not involve any harmful chemicals, making it a sustainable choice for eco-conscious individuals and businesses. By opting for in-house anodizing, you can also reduce the carbon footprint associated with transporting materials to and from professional anodizing facilities.The {} anodizing kit has already garnered rave reviews from hobbyists, crafters, and small businesses who have embraced the convenience and quality it offers. Users have praised its ease of use, reliability, and the stunning results it delivers. Some have even reported a significant cost saving compared to outsourcing their anodizing needs, making the kit a practical investment for both personal and professional use.Whether you are a passionate DIYer looking to elevate your aluminium projects or a small business owner seeking to offer anodizing services to your clients, the {} anodizing kit is a game-changer. With its user-friendly design, customizable options, and environmentally friendly approach, it is set to revolutionize the way we approach aluminium finishing. Say goodbye to the hassle and expense of traditional anodizing and say hello to the future of at-home anodizing with {}!
Innovative Engineering Solutions for Machining Design
As an AI, I cannot browse the internet for specific company introductions related to Machining Design. However, I can provide a general news content related to machining design. Here is an example of an 800-word news content:Advancements in Machining Design Revolutionizing the IndustryMachining design has been a crucial component in the manufacturing industry for decades, encompassing a wide range of processes that are utilized to shape and mold raw materials into finished products. From traditional methods such as milling and turning to cutting-edge technologies like CNC machining, the field of machining design continues to evolve and revolutionize the industry.One company that has been at the forefront of this revolution is {}. With a rich history dating back to 1980, the company has been a pioneer in the development of cutting-edge machining design solutions that have set new standards for precision, efficiency, and quality. By combining state-of-the-art technology with expert craftsmanship, {} has earned a reputation as a leader in the field of machining design.The core of {}'s success lies in their commitment to innovation and continuous improvement. The company has invested heavily in research and development, constantly pushing the boundaries of what is possible in machining design. This dedication has led to the development of advanced machining techniques that have transformed the way products are manufactured.One such advancement is the integration of computer-aided design and manufacturing (CAD/CAM) software into the machining process. This technology allows for the creation of highly complex and intricate designs, enabling manufacturers to produce parts and components with unprecedented precision and accuracy. By leveraging the power of CAD/CAM software, {} has been able to take on projects that were once deemed impossible, opening up new possibilities for their clients and the industry as a whole.Another area of innovation for {} has been in the realm of 3D printing. By embracing additive manufacturing, the company has been able to create intricate and lightweight components that were previously unattainable using traditional machining methods. This breakthrough has not only expanded the capabilities of {} but has also led to significant advancements in the aerospace, automotive, and medical industries, where lightweight and durable parts are in high demand.Moreover, {} has also played a pivotal role in the adoption of automation and robotics within the machining process. By utilizing automated machining centers and robotic arms, the company has been able to streamline production, reduce lead times, and improve overall efficiency. With the integration of these advanced technologies, {} has been able to meet the growing demands of their clients and maintain their position as an industry leader.In addition to technological advancements, {} has also prioritized sustainability and environmental responsibility in their machining design processes. The company has implemented eco-friendly manufacturing practices and has invested in energy-efficient machinery, reducing their environmental footprint while maintaining the highest standards of quality and precision.Looking ahead, {} shows no signs of slowing down in their pursuit of innovation and excellence in machining design. The company continues to invest in cutting-edge technologies, expand their capabilities, and explore new frontiers in manufacturing. With a strong commitment to pushing the boundaries of what is possible, {} is poised to shape the future of machining design and drive the industry forward.In conclusion, the advancements made by {} in machining design have not only had a profound impact on the manufacturing industry but have also revolutionized the way products are designed, produced, and delivered. By embracing innovation, technology, and sustainability, {} has cemented its position as a trailblazer in the field of machining design and continues to set new standards for precision, efficiency, and quality.
Highly Rated 3 Axis Milling Machine: A Must-Have for Precision Engineers
Famous Milling Machine 3 Axis Company Introduces Cutting-Edge TechnologyThe renowned company (brand name removed) is making waves in the manufacturing industry with its state-of-the-art milling machine 3 axis technology. This cutting-edge equipment has revolutionized the way that manufacturers approach precision machining, offering unparalleled accuracy and efficiency.The (brand name removed) milling machine 3 axis is a versatile and powerful tool that is capable of conducting a wide range of machining operations, including drilling, threading, and contouring. Its advanced 3-axis motion control system enables operators to achieve highly precise cuts and shapes, making it an essential component in the production of complex and intricate parts and components.With a robust and rigid construction, the (brand name removed) milling machine 3 axis is designed to withstand heavy-duty use in industrial settings. Its high-performance spindle and tooling system ensure smooth and reliable operation, while its user-friendly interface makes it easy for operators to program and control the machine for optimal results.In addition to its superior performance, the (brand name removed) milling machine 3 axis also boasts a range of innovative features that enhance its usability and efficiency. For instance, its advanced coolant system helps to maintain a consistent temperature during machining processes, while its automatic tool changer allows for seamless transitions between different cutting tools, saving time and increasing productivity.What sets the (brand name removed) milling machine 3 axis apart from other similar equipment on the market is its commitment to quality and precision. Each machine is meticulously calibrated and tested to ensure that it meets the highest standards of accuracy and reliability, giving manufacturers the confidence to produce parts and components with tight tolerances and complex geometries.In addition to its cutting-edge technology, the company behind the (brand name removed) milling machine 3 axis is also dedicated to providing exceptional customer service and support. With a team of highly skilled technicians and engineers, the company is able to offer comprehensive training and technical assistance to help customers maximize the capabilities of their machines and optimize their machining processes.Furthermore, the company is committed to sustainability and environmental responsibility, ensuring that its milling machine 3 axis is designed and manufactured with eco-friendly materials and processes. This dedication to environmental stewardship sets the company apart as a leader in the industry, appealing to manufacturers who are seeking to reduce their carbon footprint and minimize their impact on the planet.As a result of these innovative features and commitments to quality and sustainability, the (brand name removed) milling machine 3 axis has quickly become a favorite among manufacturers in a variety of industries, from aerospace and automotive to medical devices and consumer electronics. Its ability to deliver precise, reliable results in a fast-paced production environment has earned it a reputation as a game-changer in the world of precision machining.In conclusion, the (brand name removed) milling machine 3 axis is a testament to the company's dedication to pushing the boundaries of technology and empowering manufacturers to achieve their production goals with unparalleled precision and efficiency. With its advanced features, exceptional performance, and commitment to customer satisfaction and sustainability, it is no wonder that this milling machine has become a staple in the manufacturing industry. As the company continues to innovate and adapt to the evolving needs of the market, it is sure to remain a driving force in the advancement of precision machining technology for years to come.
Metal Machined Parts: Quality Customized Options Available
Custom Metal Machined Parts is a renowned provider of precision machined parts for a wide range of industries. With a commitment to quality and excellence, the company has built a strong reputation for delivering high-precision components that meet the exact specifications of their customers. Their state-of-the-art manufacturing facility and team of experienced engineers and machinists enable them to produce custom metal machined parts with exceptional accuracy and reliability.The company specializes in machining a variety of materials, including aluminum, stainless steel, brass, and titanium, among others. Whether it's a simple component or a complex part with intricate details, Custom Metal Machined Parts has the capability to deliver precision machined parts that meet the most demanding requirements.One of the key strengths of Custom Metal Machined Parts is their ability to work closely with customers to understand their unique needs and requirements. From the initial concept to the final product, the company's team of engineers and machinists collaborate with customers to ensure that the finished parts meet the highest standards of quality and precision. This collaborative approach enables them to provide tailored solutions that address specific challenges and requirements, ultimately leading to customer satisfaction and success.In addition to their precision machining capabilities, Custom Metal Machined Parts also offers a range of secondary services, including surface treatment, heat treatment, and assembly. These additional services complement their machining capabilities and enable them to provide complete solutions to their customers, further enhancing their value proposition.The company serves a diverse range of industries, including aerospace, automotive, defense, medical, and electronics. Their expertise in machining high-quality components has positioned them as a trusted partner for businesses in these sectors, and their commitment to excellence has earned them a loyal customer base.In a recent development, Custom Metal Machined Parts announced the expansion of their manufacturing capabilities with the acquisition of advanced machining equipment. This strategic investment is aimed at further enhancing their production capacity and capabilities, enabling them to meet the growing demand for custom metal machined parts."We are excited to announce the expansion of our manufacturing capabilities with the addition of advanced machining equipment," said the CEO of Custom Metal Machined Parts. "This investment is a testament to our commitment to providing the highest quality precision machined parts to our customers. With this expansion, we are well-positioned to meet the evolving needs of our customers and continue to be a leader in the industry."The company's continued investment in advanced technology and equipment underscores their dedication to staying at the forefront of precision machining and delivering the best possible solutions to their customers. With their expanded capabilities, they are well-equipped to take on new and challenging projects, further solidifying their position as a trusted partner for precision machined parts.Custom Metal Machined Parts' relentless focus on quality, precision, and customer satisfaction sets them apart in the industry. With their dedication to excellence and continuous improvement, they are well-positioned to continue serving the needs of their customers and delivering outstanding custom metal machined parts for years to come.
Exploring Different Metal Casting Methods in Manufacturing
Metal Casting Methods Factory, a leading provider of high-quality metal casting solutions, has recently announced the launch of their new state-of-the-art casting facility. With over 20 years of experience in the industry, Metal Casting Methods Factory has gained a reputation for delivering top-notch casting services to a wide range of industries, including automotive, aerospace, and industrial machinery.The new facility, located in the heart of the industrial district, is equipped with the latest casting technology and machinery, allowing Metal Casting Methods Factory to offer an even wider range of casting methods to meet the diverse needs of their customers. The facility features advanced melting and pouring equipment, precision molding and core making machinery, and a dedicated quality control and testing area to ensure the highest level of product quality."We are thrilled to announce the opening of our new casting facility," said the CEO of Metal Casting Methods Factory. "This investment reflects our commitment to meeting the evolving needs of our customers and providing them with the best casting solutions available in the market. The new facility will allow us to expand our capabilities and enhance our production capacity while continuing to deliver superior quality and precision in every casting project."Metal Casting Methods Factory offers a wide range of casting methods, including sand casting, investment casting, and die casting, to accommodate various design complexities and material requirements. The company's team of highly skilled engineers and technicians work closely with customers to understand their specific needs and develop customized casting solutions that meet their exact specifications.In addition to its advanced casting capabilities, Metal Casting Methods Factory also specializes in providing value-added services such as heat treatment, surface finishing, and machining to deliver fully finished and ready-to-use cast components to its customers. With a focus on continuous improvement and innovation, the company is dedicated to staying at the forefront of the industry and exceeding customer expectations.Metal Casting Methods Factory is also committed to environmental sustainability and adheres to strict standards for eco-friendly manufacturing practices. The new facility is designed to optimize energy efficiency and minimize waste, reflecting the company's dedication to responsible production and environmental stewardship.As part of their expansion, Metal Casting Methods Factory is also ramping up its efforts to serve a broader customer base and expand its reach into new markets. The company has established strategic partnerships with leading manufacturers and suppliers to ensure a seamless supply chain and timely delivery of casting products to customers worldwide.The opening of the new casting facility is a significant milestone for Metal Casting Methods Factory and reaffirms its position as a trusted and reliable partner for high-quality metal casting solutions. With its unwavering commitment to excellence, innovation, and customer satisfaction, the company is poised for continuous growth and success in the global casting industry.For more information about Metal Casting Methods Factory and its casting solutions, visit www.metalcastingmethods.com or contact [email protected]
CNC Milling Parts Manufacturers: A Complete Guide
CNC Milling Parts Factories (need to remove brand name) are known for their precision engineering and top-quality products. With a focus on providing customers with the best possible parts for their needs, these factories have become a go-to source for companies looking for high-performance components.The company utilizes state-of-the-art equipment and technology to ensure that their products meet the highest industry standards. Their CNC milling services are capable of producing complex parts with tight tolerances, making them a favorite among a wide range of industries, such as aerospace, automotive, and medical.One of the standout features of CNC Milling Parts Factories (need to remove brand name) is their ability to work with a variety of materials, including aluminum, steel, and titanium. This versatility allows them to cater to the diverse needs of their customers, whether they require parts for a lightweight aircraft or heavy-duty machinery.In addition to their advanced equipment, the company is staffed with highly skilled engineers and technicians who are experts in their field. These professionals have the experience and knowledge to tackle even the most challenging projects, ensuring that customers receive the highest quality parts every time.CNC Milling Parts Factories (need to remove brand name) are also committed to providing excellent customer service. They work closely with their clients to understand their specific requirements and offer tailored solutions to meet their needs. This dedication to customer satisfaction has earned the company a loyal and satisfied customer base.Furthermore, the company is dedicated to maintaining a high level of quality control throughout the production process. Every part undergoes rigorous testing and inspection to ensure that it meets the company's strict quality standards before being delivered to the customer. This commitment to quality has earned the company a stellar reputation for reliability and consistency.By combining cutting-edge technology, a team of skilled professionals, and a dedication to customer satisfaction, CNC Milling Parts Factories (need to remove brand name) have positioned themselves as a leader in the industry. They continue to innovate and expand their capabilities to better serve their clients, solidifying their reputation as a go-to source for high-quality CNC milling parts.As the demand for precision-engineered parts continues to grow across various industries, CNC Milling Parts Factories (need to remove brand name) are well-positioned to meet this demand with their advanced capabilities and commitment to excellence. Their track record of delivering superior products and exceptional service makes them a trusted partner for companies seeking reliable and high-quality CNC milling parts.With a focus on innovation, quality, and customer satisfaction, CNC Milling Parts Factories (need to remove brand name) are well-equipped to continue leading the way in the CNC milling industry. Their dedication to excellence and commitment to meeting the unique needs of their customers set them apart as a trusted and reliable source for high-performance parts.
5 Key Advantages of Using CNC for Manufacturers
The CNC (Computer Numerical Control) technology has revolutionized the manufacturing industry by providing numerous advantages to manufacturers. With the ability to automate machine tools and control them through a computer program, CNC technology has empowered manufacturers to achieve higher levels of precision, efficiency, and productivity. This has resulted in significant cost savings and improved competitiveness in the global market.One of the leading companies in the CNC manufacturing industry is {}. With a strong focus on innovation and cutting-edge technology, {} has established itself as a key player in the market. The company's commitment to excellence and dedication to meeting the needs of its customers have made it a trusted partner for manufacturers seeking to maximize the benefits of CNC technology.One of the primary advantages of CNC technology is its ability to enhance precision in manufacturing processes. By eliminating the potential for human error, CNC machines can consistently produce high-quality, accurate components and products. This level of precision is essential for industries such as aerospace, automotive, and medical devices, where even the smallest deviation can have significant consequences. {}Furthermore, CNC technology enables manufacturers to achieve greater efficiency in their production processes. With the ability to program complex machining operations and automate repetitive tasks, CNC machines can operate continuously without the need for manual intervention. This results in higher production rates and reduced lead times, allowing manufacturers to meet customer demands more effectively. {}In addition to precision and efficiency, CNC technology also offers flexibility in manufacturing. The ability to reprogram CNC machines for different tasks and products enables manufacturers to adapt to changing market demands and production requirements. This flexibility is particularly valuable for companies operating in dynamic industries where product designs and specifications frequently evolve. {}Another advantage of CNC technology is its ability to improve safety in manufacturing environments. By minimizing the need for manual handling of heavy machinery and reducing the risk of workplace accidents, CNC machines contribute to a safer and more secure working environment for operators and other personnel. This not only enhances the well-being of employees but also reduces the potential for costly downtime and production disruptions due to injury-related incidents. {}Moreover, the integration of CNC technology with advanced software systems allows manufacturers to streamline their production planning and control processes. By leveraging real-time data and analytics, companies can optimize their manufacturing operations, identify areas for improvement, and make informed decisions to enhance overall performance. This level of insight and control is invaluable for manufacturers seeking to achieve operational excellence and maximize their competitive advantage. {}As a leading provider of CNC technology, {} is dedicated to empowering manufacturers with the tools and resources they need to succeed in today's competitive market. Through its innovative product offerings and comprehensive support services, {} enables its customers to unlock the full potential of CNC technology and achieve sustainable business growth. The company's commitment to driving the advancement of manufacturing technologies and its focus on customer satisfaction make it a preferred partner for manufacturers around the world. {}In conclusion, the numerous advantages of CNC technology have had a profound impact on the manufacturing industry, empowering companies to achieve higher levels of precision, efficiency, flexibility, and safety in their production processes. As a prominent player in the CNC manufacturing sector, {} is at the forefront of driving innovation and excellence in the industry, supporting manufacturers in their quest for operational excellence and sustained growth. With its unwavering commitment to customer success and its dedication to delivering cutting-edge solutions, {} continues to be a trusted and reliable partner for manufacturers seeking to harness the power of CNC technology.
Injection Molding Process for DIY Enthusiasts at Home
In today's rapidly evolving manufacturing landscape, the demand for innovative and cost-effective production solutions is higher than ever. As a result, more and more individuals and businesses are turning to ODM injection molding to meet their manufacturing needs. With the emergence of advanced technologies and the ability to carry out ODM injection molding at home, the possibilities for small-scale production have expanded significantly.One company that is at the forefront of this industry transformation is {}. With its cutting-edge ODM injection molding solutions, the company has positioned itself as a leader in the field of customized manufacturing. By leveraging its extensive experience and expertise in injection molding, the company has successfully developed a range of ODM injection molding products that are tailored to meet the unique requirements of its clients.Through its innovative approach to ODM injection molding, {} has paved the way for individuals and businesses to take advantage of the benefits of in-house manufacturing. By offering a comprehensive range of ODM injection molding services, the company has empowered its clients to bring their product ideas to life with ease and efficiency. From design and prototyping to production and assembly, {} provides end-to-end ODM injection molding solutions that are tailored to meet the specific needs of its clients.One of the key advantages of ODM injection molding at home is the ability to create customized and complex parts with high precision and efficiency. By utilizing advanced injection molding techniques, individuals and businesses can produce parts with intricate geometries and tight tolerances, all within the comfort of their own facilities. This level of flexibility and control is invaluable in today's fast-paced manufacturing environment, where time-to-market and product differentiation are crucial factors for success.In addition to its state-of-the-art ODM injection molding solutions, {} is committed to delivering exceptional customer service and support. The company's team of experienced professionals works closely with clients to understand their unique requirements and provide tailored ODM injection molding solutions that meet their specific needs. Whether it's a small-scale production run or a large-scale manufacturing project, {} is dedicated to delivering superior results that exceed its clients' expectations.Furthermore, {} is a strong advocate for sustainable manufacturing practices. By implementing environmentally friendly processes and materials in its ODM injection molding operations, the company is contributing to a greener and more sustainable future. With a focus on reducing waste and energy consumption, {} is setting a new standard for responsible and ethical manufacturing.In conclusion, the growing trend of ODM injection molding at home is reshaping the manufacturing industry, and companies like {} are leading the way with their innovative solutions and unwavering commitment to customer satisfaction. With a focus on quality, efficiency, and sustainability, {} is empowering individuals and businesses to realize their manufacturing goals with confidence and ease. As the demand for customized manufacturing solutions continues to rise, the importance of ODM injection molding at home cannot be overstated, and companies like {} are at the forefront of this transformative shift.
A Comprehensive Guide to CNC Factories: Everything You Need to Know
Introduction to CNC FactoriesCNC (Computer Numerical Control) factories have revolutionized the manufacturing industry by integrating advanced technology into the production process. These factories utilize computerized systems to control and automate machine tools, resulting in increased precision, efficiency, and productivity. The use of CNC technology has rapidly expanded across various industries, leading to the establishment of advanced manufacturing facilities worldwide.One such company at the forefront of CNC technology is {Company Name}. With its state-of-the-art CNC factory, {Company Name} has set new standards for precision engineering and manufacturing. The company’s commitment to innovation and investment in cutting-edge technology has enabled it to deliver high-quality products to a global customer base.In this article, we will explore the key aspects of CNC factories, including their functionality, applications, and the impact of {Company Name}’s CNC factory on the manufacturing industry.The Functionality of CNC FactoriesCNC factories are equipped with advanced machinery and computerized control systems that enable precise and consistent manufacturing processes. These factories use CNC machines, such as lathes, milling machines, routers, and grinders, to carry out a wide range of manufacturing tasks, including cutting, shaping, drilling, and finishing various materials, such as metal, plastic, and wood.The core functionality of CNC factories lies in the ability to program these machines to perform specific tasks with high accuracy and repeatability. This is achieved through the use of CAD/CAM software, which allows engineers and operators to create detailed instructions for the CNC machines to follow. As a result, CNC factories can produce complex and intricate components with minimal human intervention, leading to improved efficiency and reduced labor costs.Applications of CNC TechnologyThe versatility of CNC technology has led to its widespread application across a multitude of industries. In the automotive sector, CNC factories are used to manufacture precision-engineered components, such as engine parts, gearboxes, and chassis components, to meet the stringent quality and performance requirements of modern vehicles. The aerospace industry relies heavily on CNC technology for the production of aircraft components, including complex geometries that require high levels of accuracy and consistency.In addition, the medical and dental industries utilize CNC factories to produce custom implants, prosthetics, and surgical instruments with exceptional precision and reliability. The electronics industry benefits from CNC technology for the fabrication of circuit boards, electronic enclosures, and intricate components for consumer electronics devices.{Company Name}’s Cutting-Edge CNC Factory{Company Name} has established itself as a leader in the manufacturing industry, with its advanced CNC factory serving as a testament to its dedication to innovation and excellence. The company’s CNC factory is equipped with a range of cutting-edge CNC machines, including multi-axis milling machines, turning centers, and precision grinders, capable of producing components with unparalleled accuracy and surface finish.Moreover, {Company Name} has invested in the latest CAD/CAM software and robotic automation systems to optimize its manufacturing processes and achieve higher levels of efficiency and productivity. The integration of these technologies has positioned {Company Name} at the forefront of CNC manufacturing, enabling it to meet the complex and demanding requirements of its customers across various industries.Impact on the Manufacturing IndustryThe implementation of CNC factories has had a profound impact on the manufacturing industry, leading to improved quality, reduced lead times, and increased production capacity. By leveraging CNC technology, manufacturers can create complex and customized components with greater flexibility and precision, meeting the evolving demands of the market.In addition, CNC factories have enabled companies to streamline their production workflows, minimize waste, and reduce operational costs, resulting in higher profitability and competitiveness in the global marketplace. The ability to mass-produce intricate parts with consistent quality has positioned CNC factories as a cornerstone of modern manufacturing, driving innovation and driving economic growth.In conclusion, CNC factories represent the epitome of modern manufacturing, combining advanced technology with precision engineering to deliver high-quality products across diverse industries. With {Company Name}’s cutting-edge CNC factory leading the way, the future of manufacturing looks promising, with limitless possibilities for innovation and growth.